Silicone Rubber Molding parts: The Solution For Material Binding Challenges
When chemical reactions between incompatible materials prevent good adhesion, silicone rubber molding can provide a solution to the dilemma. It makes it possible to bind the rubber and metal together. Some of the products in which the technology is used are vibration dampers, grommets, bellows, bumpers, tips, pulley wheels, boots, connector elbows, seals and valves.
Moreover, rubber molding manufacturers offer tailor-made parts for every design. Utilizing the expertise and experience of such a provision ensures that the end product is compatible with the application for which it will be used.
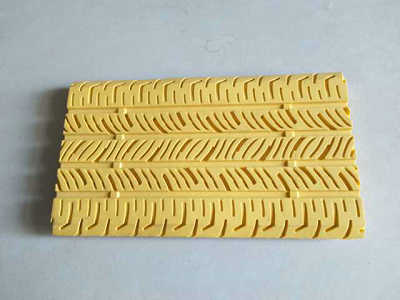
What’s more, rubber on metal and rubber on substrate precision bonding parts made in the United States offer entrepreneurs even more benefits. The Made in the USA stamp ensures a level of service and quality that foreign suppliers of rubber moldings cannot offer. With an American rubber molding partner, you no longer have to wait weeks or months for parts from China that might not even sniff when they arrive to reach your door.
There are three types of production processes for rubber moldings. This is about rubber injection molding, rubber compression molding, and rubber transfer molding. silicone rubber molding. What follows is a brief discussion of the differences between the three.
Rubber injection molding originated in the 1960s. As an extension of the plastics industry, it has evolved as a way to overcome the challenges of pressure and temperature that arose when bonding rubber. Today, it is often recognized as the most efficient means of forming a rubber. Injection molding can also be combined with transfer molding into a hybrid process.
Rubber transfer forms are another type of bond that uses compression. Parts formed in this way are made of rubber that has been compressed by a plunger. This diving action pushes the rubber into the cavity of the desired part where it assumes the intended shape. This type of rubber molding can be extremely cost-effective thanks to the possibility of using the same pre-form for multiple cavities. The only real drawback is the wasted material that remains during the transfer process. However, this rubber can be recycled for environmentally conscious entrepreneurs.
As the name implies, rubber compression molding also uses compression to achieve the desired end product. The process has been around for more than a century and has remained virtually unchanged since its inception. Like transfer molds, compression molding includes rubber preforms that are in the shape of the end product. These molds are then 1) molded, 2) the rubber is allowed to cure and finally 3) the mold is taken out of the mold. This type of rubber molding is cost-effective in three specific scenarios:
- When the business owner already has the required compression molding tools.
- When the required output is a very limited amount.
- When a large cross-sectional part must be cured for a long period. Which of these options for rubber moldings is suitable for you depends on your specific circumstances. If you are dealing with newly designed components, consult a rubber molding expert for advice on the best and most cost-effective way to solve your glue problems.